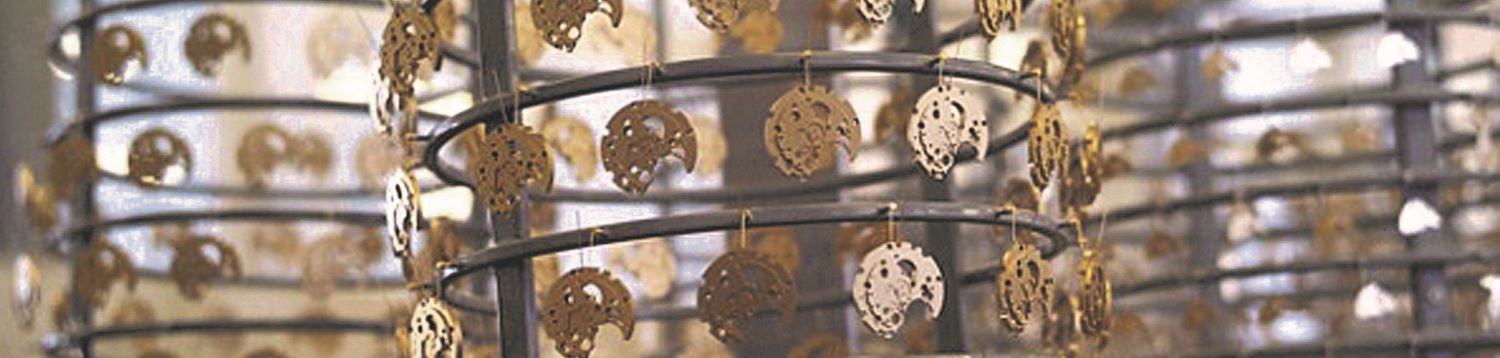
HOW TO REDUCE NON-QUALITY COSTS IN THE ELECTROPLATING INDUSTRY?
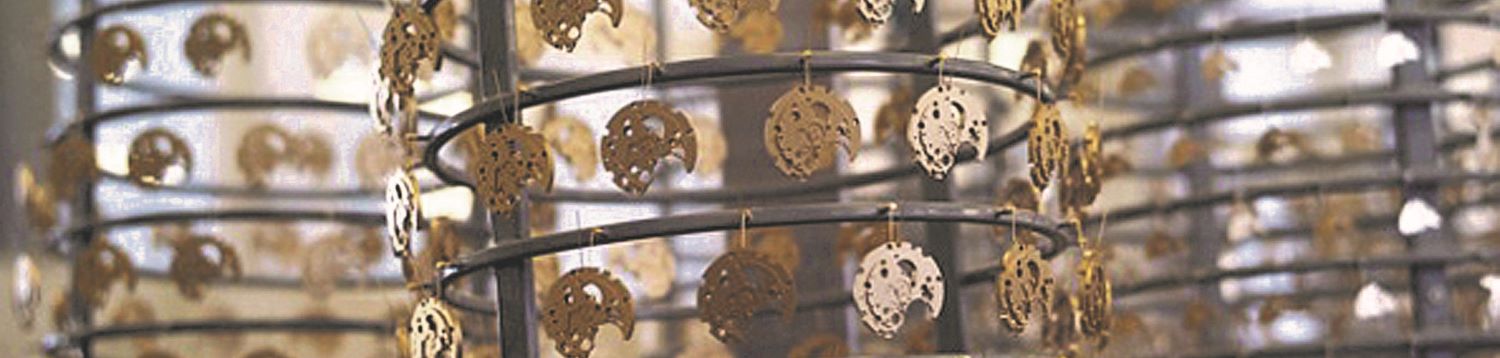
Microorganism development in rinsing baths in the electroplating industry can cause visual defects on the treated items. This kind of contamination can lead to substantial non-quality costs and production shutdowns.
To this day, few water system operators implemented monitoring procedures of the microbial development. Preventive measures are done “blind” at a frequency arbitrarily defined and without concrete follow-up. To address this contamination issue, GL BIOCONTROL developed a three-step systematic approach. It has been tested in several watchmaking factories, and companies specialized in surface treatments. Feedback on an innovative process.
Microbial contamination remains poorly known by operators
When a new production unit is installed, the water system is generally properly thought: the water pipes are new and clean with smooth surfaces, and maintenance procedures are well defined. All the ingredients required to ensure a high-quality production.
However, over time, we often observe drifts in the system. Several problems can appear:
- Modifications of the water system leading to dead legs.
- Selection of a few bacteria due to repeated treatment. Indeed, common prevention mainly relies on biocides such as isothiazolone, only biocide compatible with the surface treatment processes. Over time, this treatment can lead to the selection of a resistant flora.
- A cleaning and disinfection strategy not adapted to the water system. A too short contact time and/or a weak biocide concentration lead to ineffective biocide treatments.
- Appearance of corroded spots or scaled areas in the pipes and baths. This induces microorganism adhesion and biofilm formation.
- A high turbidity, often due to a closed loop water recycling system, that limits UV efficiency.
All these parameters lead to microbiological development in the water system and in the rinsing baths.
This microbial contamination has a negative impact on the quality of the treated items. Besides, the facility’s manager suffers a dual financial penalty: costs related to production defects (batch recalls…) and costs induced by production shutdowns to clean and disinfect the unit. Without mentioning the negative effect on the brand image…
The need of the electroplating sector is dual: ensuring the good microbiological quality of the treatment baths while limiting the maintenance costs.
A three-step approach
At GL Biocontrol, we developed a systematic approach in order to secure the manufacturing process. This solution, organised in three stages, answers to the industrial needs and optimises the corrective actions.
Identify…
The first step aims to map the water circuits in order to identify in real-time the areas under control and the critical areas. This thorough inspection highlights the circuit’s components producing biomass. To be as responsive as possible, we use a measuring tool that gives you the result directly on the field: quantitative ATPmetry. The delay, inherent to the cultural methods, is thus avoided. The production water system, the treatment baths as well as the surfaces must be analysed.
Mapping detects the critical areas of the circuit. Since then, the operator can implement the correctives actions to improve the microbiological quality of the process.
…Assess…
Next, these corrective actions must be monitored over time and assessed. For example, the various stages a treatment procedure (cleaning and disinfection) are assessed and optimised in real-time. The goal of this second step is to adjust the treatment to the ecosystem encountered to ensure an optimal efficacy. In this way, we durably limit microbial growth and biofilm formation.
…Monitor
Finally, the third and last step aims to monitor over time the evolution of the production unit microbiological quality. Using ATP tests, one can self-monitor its water circuits, the electroplating and rinsing baths. Service technicians can perform themselves the sampling and analysis on a regular basis. Implementing a biomonitoring will allow you to control in real-time the microbiological activity of the circuits. In this way, it is possible to react immediately in case of a significant increase of the microorganism level. The operator starts the earlier corrective actions to limit non-conformity on the treated parts. Besides, using an indicator of biocontamination will allow you to trigger the cleaning and disinfection procedures only when needed.
Personalized support and follow-up
GL Biocontrol offers a complete provision of expertise of the water systems and treatment baths. We also supply you with all the reagents, consumables and measurement device required for monitoring the microbial quality.
Furthermore, the offer comprises a personalized support covered by our experts to ensure that it is properly implemented: handling of the ATP tests, definition of the surveillance limits, determination of the corrective actions, etc…
To sum up…
The DIADEM approach has many advantages for production units in the sector of surface treatments. Optimisation of the microbial quality of the water and baths, as well as the implementation of a self-monitoring by ATPmetry will allow you to:
- Reduce production costs (avoid production shutdown, limit volumes of treatment products used, reduce the C.I.P procedures)
- Reduce non-quality costs due to visual defects on the treated items.