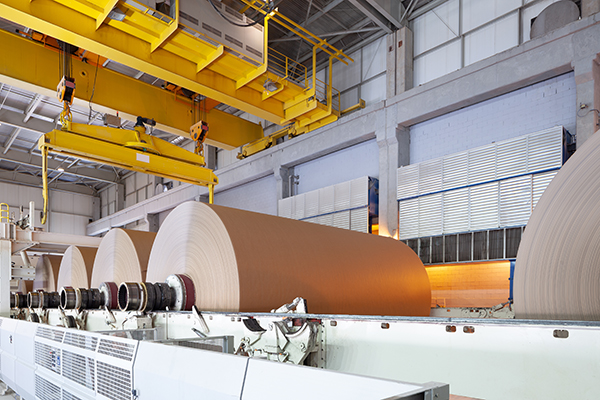
As a significant water consumer, the paper industry has adapted by reusing its industrial water. Yet, it still faces significant microbiological challenges leading to various direct and indirect consequences. These include the quality of the final product, microbial safety, environmental concerns, staff well-being…
How can the paper industry address these problems, and what solutions are available?
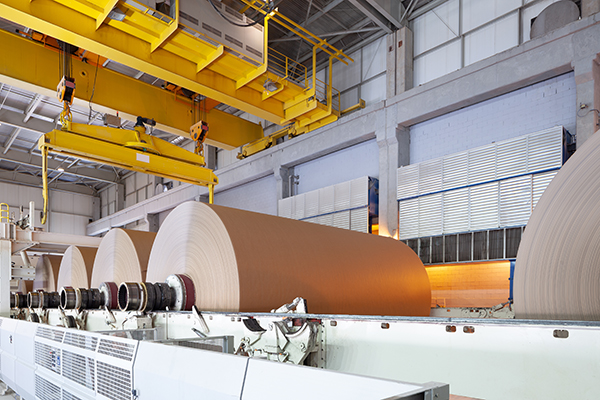
Microbiological Challenges in the Paper Industry
The paper industry’s water demand is substantial, estimated at 500 liters per kilogram of paper produced [1]. To address environmental concerns related to resource scarcity and better manage their effluents, the industry has adapted by recycling 95% to 98% of water used internally [2]. However, the closed-loop systems have intensified microbiological issues.
Indeed, microorganisms such as bacteria, yeast, and fungi find an ideal environment for rapid growth within the paper production process. Various factors, including abundant nutrients, suspended solids (MES), temperatures ranging from 30 to 60°C, and a neutral pH level (6.5 to 7.5), provide favorable conditions for microbial development.
When microorganisms grow uncontrollably, they form biofilms (slime) that adhere to machinery surfaces. This biofilm accumulation can lead to several detrimental effects:
- Weakened paper sheets causing breaks: the biofilm deposited on the paper web during the drying process creates holes, reducing paper strength and resulting in costly downtime.
- Unwanted discoloration or staining of the paper: different microorganisms present can cause grey, yellow, or orange stains, diminishing the product’s value and even rendering it unsellable.
- Unpleasant odors: microorganisms produce foul-smelling gases, leading to workplace discomfort, health issues, and neighborhood complaints.
- Microbiological corrosion: development of corrosive bacteria, like sulfite-reducing bacteria, damages networks, leading to significant maintenance costs.
Existing Curative Solutions
To prevent or address these issues, paper industry operators resort to heavy treatments that have significant environmental implications. The two main curative actions are:
- Circuit cleaning using biodispersant products, followed by total network drainage.
- Disinfection with biocidal products, which can be harmful to the environment.
However, these methods come with consequences:
Curative actions | Consequences |
Cleaning | Filamentous bacteria discharge in wastewater treatment plants An excessive growth of filamentous bacteria leads to bulking phenomena, affecting sludge settling. This degrades the quality of the discharged effluent. |
Biodispersants discharge in wastewater treatment plants In large quantities, these products are difficult to eliminate and/or neutralize. Their release into the natural environment can cause environmental problems. |
|
Disinfection | Biocide discharge in wastewater treatment plants Biocidal substances are challenging to eliminate completely, resulting in their release into the natural environment, causing environmental issues. |
Residues in mists enveloping the machine
A health risk (Legionellosis) for employees working in the manufacturing facility. |
|
Significant economic cost in biocide products for the company |
Mastering Product Treatment Usage is Achievable!
While product treatment remains essential for ensuring high-quality production and safety, controlling the quantity of used products is necessary to limit toxic agent discharge into the environment.
One solution to reduce product usage is to prevent biofilm development proactively. Regularly monitoring the water network allows operators to anticipate microbiological issues, biofilm accumulation, and subsequent product contamination. In this regard, having a total flora indicator is essential. Quantitative ATP-metry provides on-site results in just 2 minutes, indicating the overall microbiological load of water. This enables operators to take action before defects appear in the final product.
ATP tests offer several advantages, including:
- Identifying process elements that are sources of contamination or microbial growth, facilitating targeted antimicrobial treatments.
- Evaluating the effectiveness of existing biocidal treatments.
- Improving treatment efficiency through better selection of active molecules, injection points, and frequencies.
- Anticipating potential microbiological issues.
ATP tests thus provide numerous benefits:
- Reduced production defects.
- Decreased installation downtime.
- Limited use of environmentally harmful products, promoting eco-responsible management of biocidal and biodispersant products – use only what is necessary!
- Cost savings on treatment products.
In conclusion, by employing advanced techniques such as ATP-metry, the paper industry can overcome its microbiological challenges more effectively, ensuring high-quality production while maintaining a sustainable approach to environmental and economic factors.
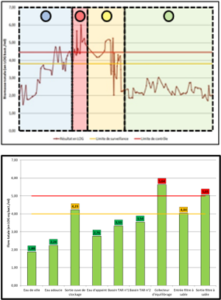